This could range from ensuring a simple product like our isolation ball valves are ‘full bore’ to ensuring minimum pressure requirements in our control valves, like the PICV.
Whether we believe in global warming or not, whatever the reason for energy saving, surely if there is a better way of doing it that uses less resources, energy or materials, then we should be doing it.
There are many reasons that system designers, building owners and occupants look to achieve energy savings.
These could include;
- Reduction in energy costs
- Reduce CO2 ‘footprint’
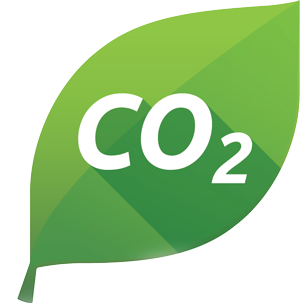
Valves are a relatively small part in the overall mechanical installation, but (and it’s a fairly big but) the efficiency of the total system depends on the correct selection, installation and commissioning of valves.
The satisfaction of completing a jigsaw puzzle is only achieved when all the correct pieces are interlinked forming the finished picture, as with a mechanical installation, all the component parts are interlinked and dependent on each other.
Compromising on just one single installed item within a system could compromise the whole end result, ie efficiency, whole life costs and comfort control for the occupants.
If we consider the role commissioning and control valves play in a typical (if there is such a thing) chilled water application, we see how valves influence system efficiency and pump energy use.
Correctly selected, installed and commissioned valves help achieve;
- Higher Chiller Efficiencies
- Pump Energy Savings
Chiller Efficiency
The Problem
In simple terms, the chiller efficiency is a measure of productivity, ie what you get out compared with what you put in. The concept of the ‘getting out’ and the ‘putting in’ are fairly simple, ie a measure of heat output compared to the energy input; easy to measure and equate to a value. The design type and build quality of the chiller will have an efficiency value.
Not all the energy input can be converted to the heat output, there are always losses. A major contributor to the efficiency of the chiller is the return temperature of the system water. Chillers operate at maximum efficiency when the required delta T (ΔT), ie the differential temperature between flow and return water, is achieved. Returning water at a lower temperature than the design requires reduces the overall running efficiency of the chiller.
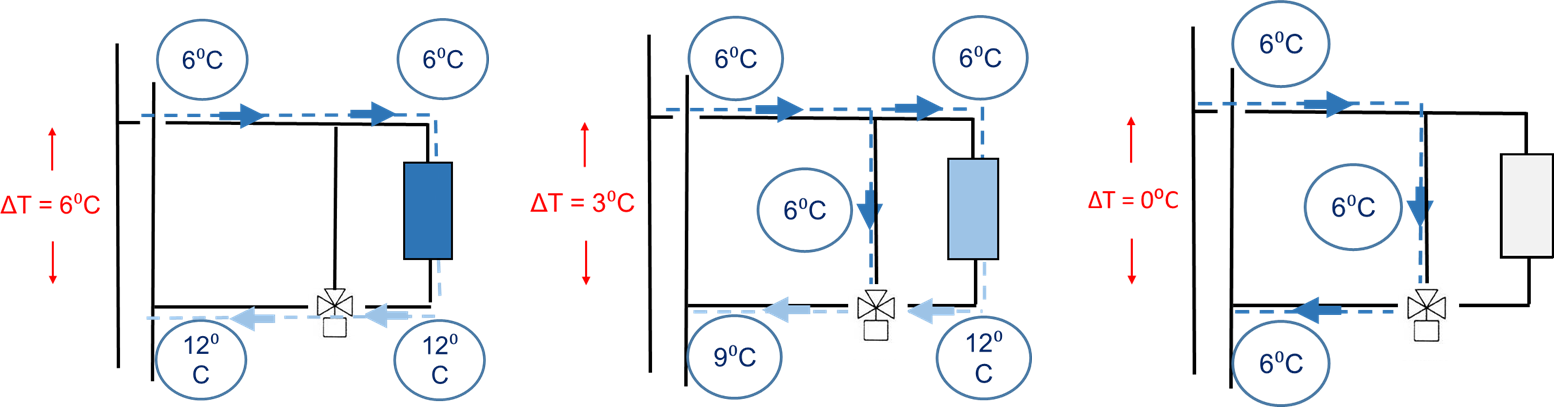
This is commonly referred to as ‘Delta T Syndrome’.
The Solution
Initially, the 3 or 4 port control valves were changed to 2 port control valves, this allowed the return water temperature to be controlled. The function of 3 and 4 port control valves is to bypass the supply water, at the supply temperature, directly into the return pipework. Bypassing the supply water reduces the return water temperature to the chiller, therefore reducing its efficiency. The installation of 2 port control valves resolved this issue, provided that its control authority was high enough, typically greater than 0.5.
Within variable volume systems however, 2 port control valves need to be protected from fluctuating system pressures. Initially, DPCVs (Differential Pressure Control Valves) were installed to ‘protect’ the authority of the 2 port control valves. More recently, PICVs (Pressure Independent Control Valves) were introduced to replace the 2 port control valve, DPCV and commissioning valve. Installing PICVs reduces installation and commissioning time, as well as the quantity of installed valves. PICVs have a control authority of 1.0, therefore, are the final piece in the installation efficiency ‘jigsaw puzzle’.
Pump Energy
The change to 2 port control valves which are protected by DPCVs, or to PICVs, allows for the installation of more intelligent systems, ie systems that can match supply to demand.
Systems now only create and supply enough chilled water to match the demand of the building at any point in time, and can respond to changes as comfort control demands during the day.
By matching supply to demand, systems now run for the majority of the time below maximum output, allowing for reductions in water flow rates.
It is the reduction in flow rates that allows pump energy savings to be realised.
If we look at a pump selection
- we see that pumps are selected to be capable of achieving the maximum design flow rate (100% DFR) against the ‘index’ (least favoured) circuit
- as flow rate reduces to 50% the system resistance reduces to 25%.
If we now consider the impact on energy
- we see that as the flow rate reduces to 50% and the system resistance reduces to 25%, the energy consumption reduces to 12.5%, ie an 87.5% reduction.
- we understand there are of course efficiencies within the pump to consider which reduces the actual energy savings, but savings of up to 80% are achievable.
By installing DPCVs with 2 port control valves or PICVs we can reduce flow rates to match demand, which allows the pump speed to reduce, thus lowering the pump energy consumption.
In Summary
- by changing the control valves to 2 port or PICVs, the return water temperature is kept higher, which in turn improves the chiller efficiency
- the DPCVs or PICVs control the fluctuating system pressures caused by changes in flow rates as system demands for comfort control varies during the day
- reduction in flow rates allows the pump to be run at reduced speeds, thereby saving energy.