A regular and repeating conversation, I have, across the industry, is one regarding the suitability of chemicals when used with certain metals.
This is a notoriously difficult question to answer, mainly due to compounds.
In chemistry, a compound is a substance made of two or more elements chemically bonded to each other in a fixed ratio. The chemical bonds between atoms of elements involve a transfer or sharing of valence of electrons. This gives a compound different properties from its elements. A compound may be represented by a chemical formula that shows the element symbols of the atoms and their proportions.
The number of chemical compounds that exist is not known exactly, but estimates range from 10^18 to 10^200 – for clarity, the latter is a 1 with 200 zeros after it (also known as a Googol and is a pretty big number).
According to the Chemical Abstracts Service, the CAS REGISTRY (SM) contains more than 90 million unique organic and inorganic chemical substances, such as alloys, coordination compounds, minerals, mixtures, polymers and salts, and more than 65 million sequences. Globally, more than 350,000 chemical compounds (including mixtures of chemicals) have been registered for production and use. There are millions of chemical compounds known, and many more millions are possible but have not yet been discovered or synthesized.
The reason this is so pertinent is, when a system is dosed, the use (and combination) of chemicals therein is of paramount importance.
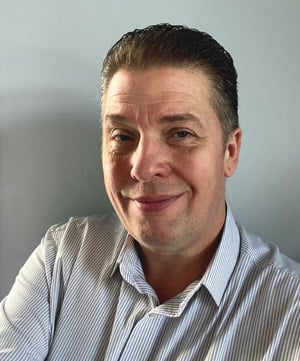
By Darren Westwood
Group Quality Director
Crane Building Services & Utilities
Chemical Suitability
Some chemicals are suitable for use across a wide range of metallic and non-metallic (such as polymeric) materials but, just because a chemical works on, for example, stainless steel, does not mean it will be suitable for us with other metals, such as brass or bronze.
One such chemical, and the primary reason for me writing this article, is Silver Nitrate and, whilst thinking of compounds, Silver Peroxide.
Silver Peroxide is a compound of Silver Nitrate and Hydrogen Peroxide – it was developed in the early 1970’s by a Mr Hungerbach in Germany.
Used correctly, with compatible materials, it can have advantages, such as:
- Long term effectiveness.
- Effective even in low concentrations (disinfection will require a long time) .
- Effective in a wide range of temperatures up to the boiling point.
- Gentle to the skin.
- Biodegradable with the exception of silver-nitrate.
- No build-up of resistance by micro-organism.
- Colourless, odourless and tasteless.
However, the disadvantages arguably outweigh the advantages:
- Silver in the form of silver-nitrate (most toxic form of silver). Silver-nitrate is one of the most toxic forms of a heavy metal, surpassed only by mercury and thus has been assigned to the highest toxicity class, together with cadmium, chromium (VI), copper, and mercury
- Silver precipitates out in contact with chlorites (salts/minerals) – generally speaking cannot therefore be used with ground water.
- Restriction on use of silver in drinking water – in the UK, it is no longer allowed for continual dosage.
- Poor disinfection at temperatures of 10°c and lower.
- Slow disinfection at low dosage.
- Silver remains in system and/or environment.
- Cannot be used in contact with copper.
This is not in any way limited to a particular manufacturer nor product type – any copper based product will degrade when in contact with Silver Peroxide – the only real variable is time (related to concentration, section thickness, location, environmental conditions, etc, so is very hard to predict).
The effect of this exposure is Stress Corrosion Cracking (hereafter referred to as SCC).
Stress Corrosion Cracking
Three factors are required for stress corrosion cracking to occur: a susceptible material is exposed to some level of applied stress and a corrosive species within the heating system (such as a substance or liquid), causing a crack to form within the material.
At first, these cracks are very small, embryonic fractures that can only be seen under a microscope, called fine branch cracking (Photos B and G below).
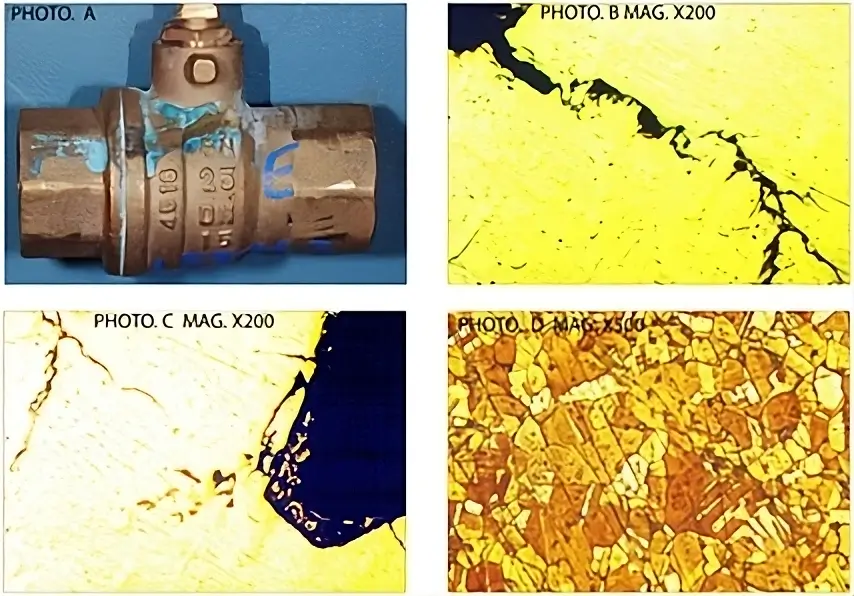
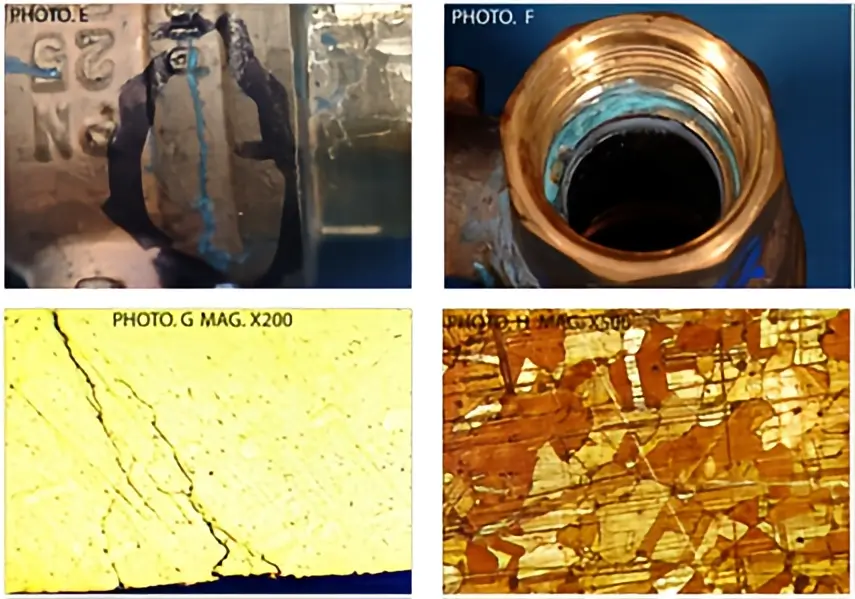
When that part is then subsequently placed under further stress, the material cannot cope with the additional loading and the material fails, often suddenly and disastrously. However, this type of failure is not the same as a part being manufactured to poor quality standards. Instead, it is usually caused by an additive being used within a system which is incompatible with the pipes and fittings. A metallurgist can identify the different failure mechanisms through the different patterns that are caused within the material.
A material fatigue failure, for example, will have a clamshell pattern with fatigue striations, which indicates the cyclic nature of fatigue and creates a visibly different crack to the fine branch cracking caused by stress corrosion cracking (see image below).
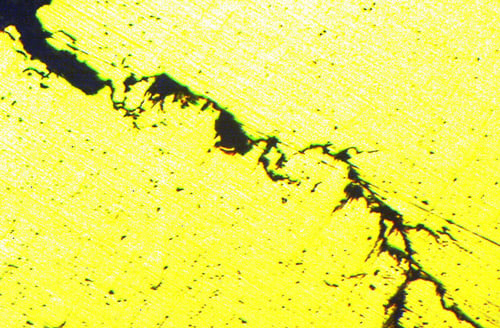
An example of fine branch cracking within a material, which is indicative of stress corrosion cracking.
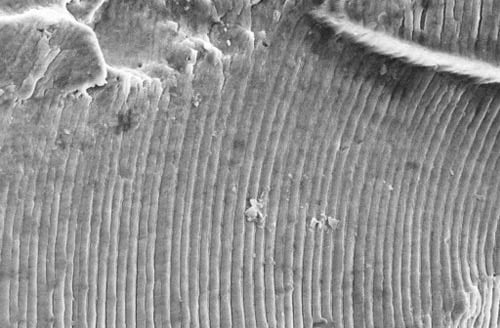
Fatigue striations are present when a material has failed, which are noticeably different to stress corrosion cracking.
Often, this type of failure happens with copper and copper alloy (brass and bronze} valves, as these materials are susceptible to corrosion.
Every installation that joins two parts together will be subject to some stress, so all that is required to create the perfect conditions for stress corrosion cracking is a corrosive substance. One of the most commonly used additives for system dosing, that has been a factor in many cases of stress corrosion cracking, is silver peroxide.
Galvanic Corrosion
Finally, and just to complicate matters further, Galvanic Corrosion may be present in poorly maintained systems.
For Galvanic Corrosion to take place, there has to be 2 factors interacting – dis-similar metals and the presence of an electrolyte.
- On the galvanic series, Stainless Steel is more noble than Carbon Steel, Cast Iron, Bronze and Brass so it is these, less noble, materials that could corrode and not the Stainless Steel pipework. When two metals are submerged in an electrolyte, while also electrically connected by some external conductor, the less noble (base) will experience galvanic corrosion.
- Dissolved gas / oxygen acting as the electrolyte.
Dis-similar materials have always been used in pipework systems, however, with the use of Stainless Steel pipework becoming more widely used in building services, the problem has increased.
Closed pumped systems, i.e. heating and chilled water, will not suffer from Galvanic Corrosion, although dis-similar materials are used, provided that the dissolved gases are removed and correct inhibitors added.
In summary, it is simply not possible to indemnify the use of Silver Nitrate nor Silver Peroxide in a mixed metal system where copper alloy materials are in use (the risk of galvanic corrosion notwithstanding).
Anyone who tells you different should have their view taken with a very large pinch of salt.